By 2023, the global logistics market is predict to have a value of $1374 billion, exhibiting a CAGR (Compound Annual Growth Rate) of 2.7% during 2018-2023.
Although these numbers might be slightly affect because of the ongoing pandemic, it does not alter the fact that the logistics company is crucial to the economy of any country.
The logistics sector employs millions of people globally, and this article focuses on the role of the distribution manager. It talks about the job description of a distribution manager. How his duties have changed with the influence of technology on the sector.
Table of Contents
The Impact of Digital Technologies on Distribution Management
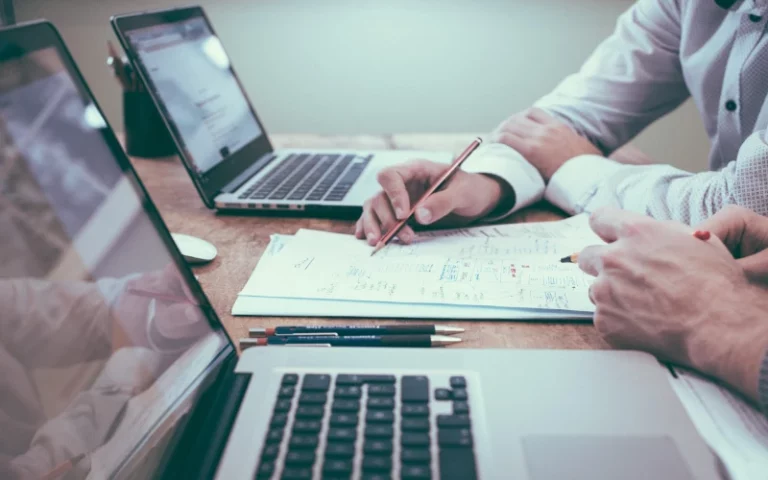
The life of a distribution manager in the era of digitization is markedly distinct from what it was just a decade ago. The rise of digital technologies has transformed how distribution managers do their jobs. It make it more comfortable to manage the supply chain and improve customer satisfaction.
One of the primary advantages of digitization is that it has made it possible to collect and analyze data in real time.
It means that distribution managers can now watch the movement of goods through the supply chain and determine potential blockages or issues before they become significant problems.
They can also use this data to optimize routes, reduce delivery times, and confirm that products are deliver to clients on time and in good condition.
Digitization enables distribution managers to use digital platforms for affordable communication with suppliers, manufacturers, and retailers, ensuring quick issue resolution through better coordination.
Digitization has also made it more comfortable for distribution managers to follow inventory levels and manage stock. They can use digital platforms to observe inventory levels in real-time and ensure they have enough stock to fulfill customer demand. It can help lower costs associated with overstocking or understocking and confirm that customers can always find the required products.
Finally, digitization has made it more comfortable for distribution managers to respond to varying customer needs and preferences. Using digital platforms to gather customer behavior and select data, they can quickly identify trends and adjust their strategies accordingly. It can help to enhance customer satisfaction and drive sales.
In short, the life of a distribution manager in the era of digitization is faster, more data-driven, and more customer-focused than ever before. With the proper tools and strategies, distribution managers can use digitization to simplify operations, reduce costs, and deliver better customer results.
What is the Role of a Distribution Manager?
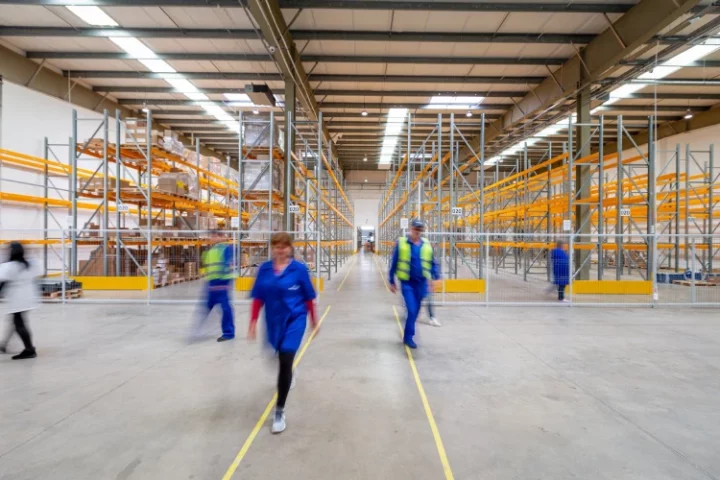
A logistics or distribution manager’s primary role is to organize the safe and efficient storage and distribution of goods from the pickup point to the destination.A distribution manager organizes shipments, oversees fleet software to manage timings and costs, and suggests improvements.
As you can imagine, the transportation network is active throughout the day across the nation. The distribution manager can’t be expected to have a 9-to-5 job. Being a distribution manager can be incredibly challenging.
Technological advancements in the logistics sector have made their jobs more accessible to some extent. Let’s explore some of the daily tasks and how technology plays a role in each.
A distribution manager oversees the movement of goods from manufacturers or suppliers to customers. They play a vital role in ensuring that products are produced on time, in good condition, and at the right price. Their responsibilities include:
- Managing inventory levels.
- Coordinating with suppliers and retailers.
- Optimizing transportation routes.
- Ensuring compliance with regulatory requirements.
They must also stay current with the industry’s most delinquent trends and make strategic decisions based on varying customer needs and preferences. In short, distribution managers are essential to the smooth operation of the supply chain and the success of any business that relies on the timely delivery of outcomes to customers.
A Day in the Life of a Distribution Manager
1. Fleet Management
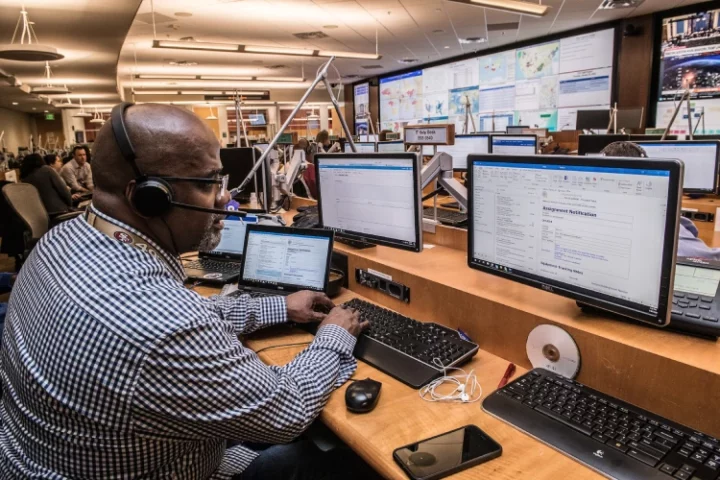
Fleet management is managing a company’s fleet of vehicles, such as cars, trucks, and vans, efficiently and cost-effectively. The goal is to maximize the lifespan and utilization of each vehicle while undervaluing operating costs, lowering fuel consumption, and ensuring compliance with regulations.
Fleet managers survey vehicle performance, schedule maintenance, and repairs, manage fuel consumption and optimize routes to improve efficiency. They also need to ensure the safety of drivers and other road users and maintain accurate records of vehicle usage and expenses. Effective fleet management is essential for any business that relies on transportation to deliver products or services.
Fleet management involves many functions like vehicle maintenance, finance, vehicle diagnostics, driver management, etc. It means ensuring that the risks and costs associated with transportation are minimized, and efficiency is maximized.
The use of telematics has proved helpful in this domain, particularly in the vehicle and asset tracking. GPS trackers are installed on vehicles and containers/trailers, and goods are transported continuously. It gives data regarding the location, vehicle speed, idle time, and so on.
These help a distribution manager follow the vehicle (and the goods) and ensure it reaches the destination safely and on time.
2. Fleet Management Software and IT
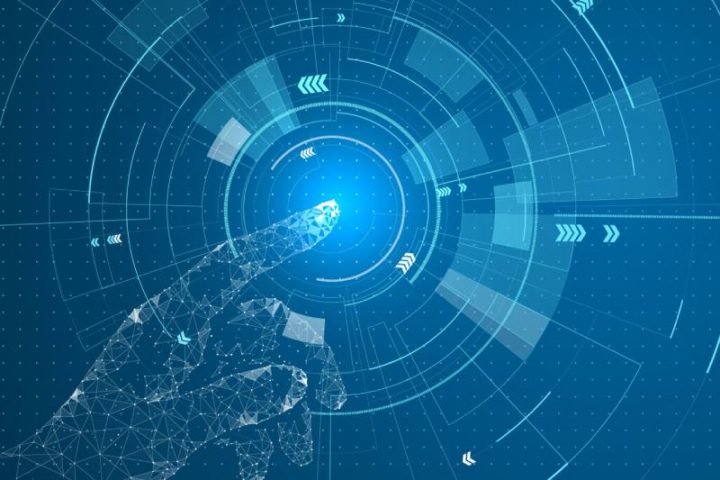
Fleet management software and IT play a critical role in modern fleet management. These technologies have revolutionized how fleet managers observe and control their fleets, enabling them to make more informed decisions and enhance operational efficiency. Fleet management software delivers real-time tracking of vehicles, optimizing routes, reducing fuel consumption, and improving driver safety.
The software also delivers insights into vehicle performance and maintenance, allowing managers to recognize potential issues before they become significant problems. Fleet management software and IT have become critical tools for businesses to manage fleets effectively, lower costs, and improve customer satisfaction.
As mentioned before, the primary purpose of using software for fleet management is to collect, process, and export information. Vehicle tracking is the actual application of technology in logistics, but together with IT, a distribution manager can achieve so much more.
How does software help in the reduction of costs? By collecting and maintaining data about the vehicle’s performance and engine, the artificial intelligence system in the software can predict when the following repair/service is due. Regular and proper maintenance of trucks prevents accidents and delays in delivering goods.
3. Driver Management and CSA
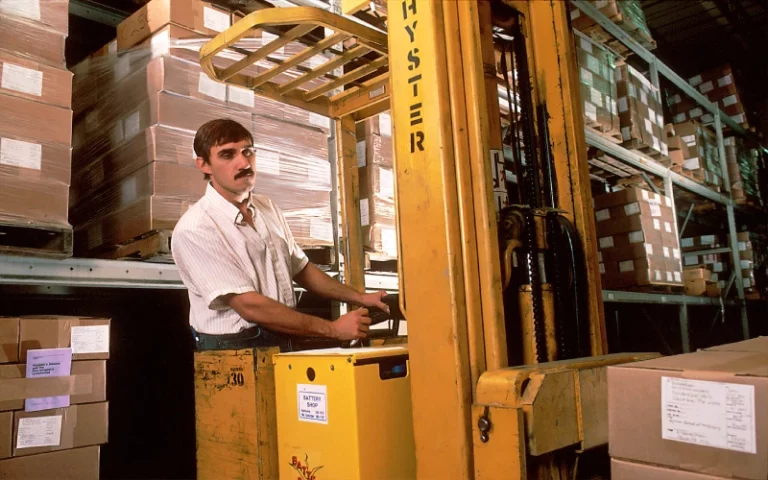
Driver management and Compliance, Safety, and Accountability (CSA) are essential aspects of fleet management that concentrate on ensuring the safety of drivers and other road users.
It involves hiring, training, and monitoring drivers to confirm they comply with regulations, obey safe driving practices, and sustain high professionalism.
CSA is a program created by the Federal Motor Carrier Safety Administration (FMCSA) that seeks to reduce commercial motor vehicle accidents by encouraging compliance with safety regulations. CSA measures driver and carrier performance based on several factors, such as breaches, accidents, and assessment results, and assigns a score that impacts their safety rating.
Effective driver management and CSA programs can enhance driver safety, decrease accidents, and assure compliance with regulations, resulting in a more secure and efficient fleet.
4. Warehouse Management
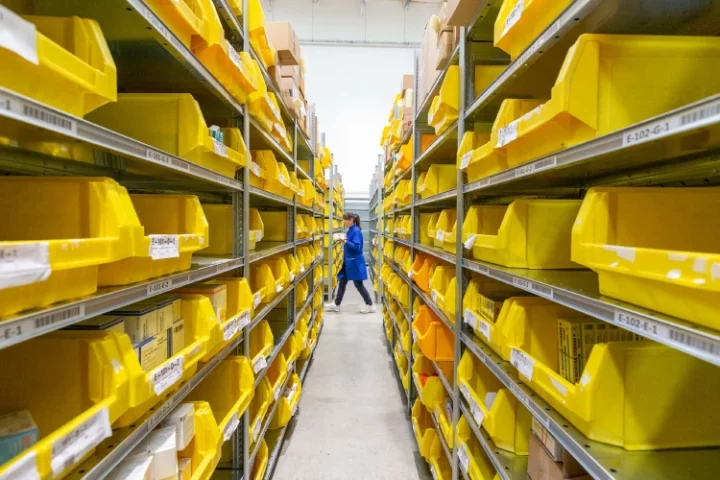
Warehouse management involves efficiently planning, organizing, and controlling the warehouse and moving goods within a warehouse. It includes accepting and processing incoming stock, managing inventory levels, picking and packing orders, and shipping products to customers.
Effective warehouse management must use technology such as warehouse management systems, barcode scanners, and inventory tracking software. It also involves personnel management, including hiring and training staff, providing safety protocols are in place, and optimizing workflows to maximize efficiency. Good warehouse management techniques help ensure the timely delivery of products, accurate inventory tracking, and cost-effective use of warehouse space.
5. Diagnostics and Analysis
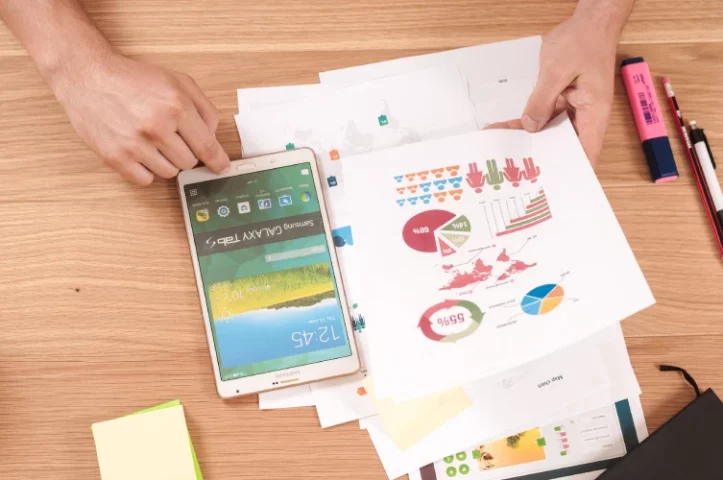
The data collected by the various devices and sensors installed on the fleet are very useful to perform data analysis to streamline and improve future transportation services.
For example, in case of an accident, the footage obtains from the truck dash cam to analyze what went wrong .
Diagnostics and analysis are:
- The methods of identifying problems.
- Determining the reason for the issues.
- Developing solutions to address them.
It involves gathering and analyzing data to comprehend the nature and extent of the problem.
The data can be managed through various forms, such as surveys, interviews, and observations. The analysis involves determining the data’s patterns, trends, and relationships to help diagnose the problem. Once the problem has been diagnosed, solutions can be designed and implemented to address the issue.
Effective diagnostics and analysis are essential for identifying and resolving problems, improving performance, and reaching organizational goals.
An Important Role of distribution manager
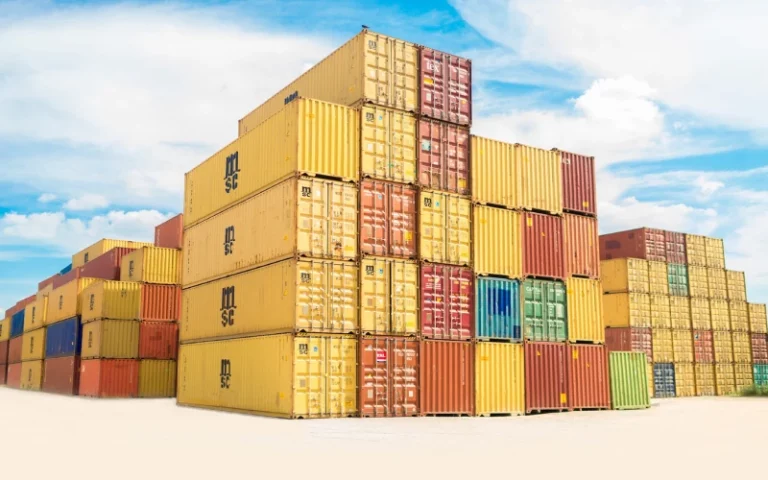
The role of a distribution manager is to control the movement of goods from the manufacturer to the end consumer. An essential responsibility of the distribution manager is to guarantee that the products are delivered to the right place, at the right time, and in a suitable condition. It involves managing transportation logistics and inventory levels and coordinating with different departments, such as sales and marketing. The distribution manager must also observe and analyze market trends to make informed conclusions about distribution strategies. The distribution manager recreates a crucial role in ensuring customer satisfaction, maximizing sales, and optimizing the supply chain to reach organizational goals.
Frequently Asked Questions
Digitization has transformed the distribution landscape by introducing new technologies and automation tools. This has increased efficiency, reduced costs, and improved customer service. The distribution manager now has access to real-time data, analytics, and automated systems to streamline the distribution process.
A distribution manager in the era of digitization should possess skills such as data analysis, problem-solving, communication, and adaptability. They should be able to leverage new technologies, manage virtual teams, and navigate complex supply chains.
Digitization enables distribution managers to track customer preferences and buying behavior, which can help them to anticipate demand and optimize inventory levels. Automated systems can also facilitate faster order processing, shipping, and delivery, resulting in better customer service.
One of the main challenges is the need to adapt to new technologies and systems, which may require additional training and resources. Additionally, data security and privacy concerns can arise, and the distribution manager must ensure compliance with regulations and standards.
A distribution manager can stay up-to-date by attending industry conferences, networking with peers, and following relevant publications and thought leaders. It is also important to work with technology vendors and partners to leverage new tools and systems. Regular training and professional development can also help to build digital skills and knowledge.